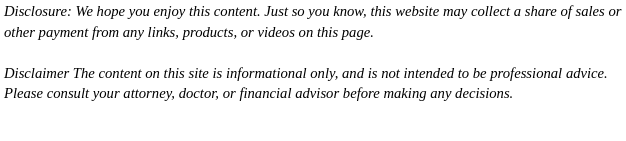

Anyone who has ever watched a loved one become seriously ill or experienced severe health problems themselves can testify that the effectiveness of sterile products and medical equipment is vital to a patient’s health. Medical devices often form a barrier between fluids or gases that could be dangerous to patients or handlers if the substances were to mix. Additionally, if a leak occurs along a pathway, the necessary medical fluids could be delivered to the wrong part of the body, or bodily fluids could gather inside the patient, creating two highly consequential situations. This concern is heightened by the fact that most medical must use flexible, elastic pieces that are susceptible to damage. For this reason, most pharmaceutical companies and medical manufacturers use leak test equipment or even hire leak testing specialists to ensure that their devices meet quality standards that will protect their patients.
Leak testing services are common in a number of industries, including automotive and refrigeration manufacturing, as a method of preventing costly leaks and creating a guarantee of merit. Leak testing methods are also often required by the American Society of Testing and Materials (ASTM) and the Food and Drug Administration (FDA). In these various leak tests, the equipment measures leak flow, which describes the leak of viscous gases and liquids, as well as slip and molecular flow. This can be extremely helpful in ensuring that medical equipment releases medication at a mandated rate, without seeping through holes or faults in the system.
Medical products, like many products, often require custom testing services to ensure consumer safety and item quality. However, medical products also set standards for sterility to further protect their patients. This can often mean a lengthy sterilization process: ensuring that a product is aseptic to qualify for patient use depends on the effectiveness of the sterilization technique, the unit design, decontamination, careful disassembling and packaging of the device, monitoring, sterilant quality and quantity, and more. In addition to this process, leak testing services differ based on the product their construction: while an IV bag, for example, requires extensive testing to ensure proper quality and sterility, its leak testing procedures will differ greatly from other devices. A small device called an Incor axial ganz poses a particular challenge due to connections at the port and tubing sections, as subtle leaks can cause fluctuations in volume that can distort leak detection results and change the pressure in the object’s interior. However, without these difficult tests and services, many patients would be unable to access the medication and treatment they need. For this reason, leak testing services continue to add new procedures and methods to further improve the safety, sterility, and quality of their field. For more about this, go here.